3 Points You Can't Miss on the Small Pixel Pitch LED Display Market!
After years of development, China's LED display industry has begun to enter the stage of deep adjustment, from the initial extensive competition to the competition of comprehensive strength represented by capital and technology. Affected by the economic environment of Sino-US trade, high market saturation and overcapacity, the growth rate of the LED display market slowed down, starting from incremental competition to stock competition. In 2018, China's LED display market is about 60 billion yuan, with a growth rate of around 17%, which is a year-on-year decline compared with the year-on-year growth rate of 26.9% in 2017.
Although the LED display industry has entered a period of gradual growth, the small pixel pitch LED display has become the main force in the development of the LED display industry in recent years, leading the industry to enter the development trend of the blue ocean market, with a small pixel pitch in just five or six years. LED display has experienced several times of rapid growth, and will continue to maintain high growth in the future, becoming a well-deserved "black horse" in the development of LED display industry. According to industry statistics, the market size of China's small pixel pitch LED display in 2017 is about 6 billion yuan. It is estimated that the market size will reach 17.7 billion yuan by 2020. Not surprisingly, the small pixel pitch LED display will occupy the commanding heights of the entire LED display industry for a long time, leading the development direction of LED display.
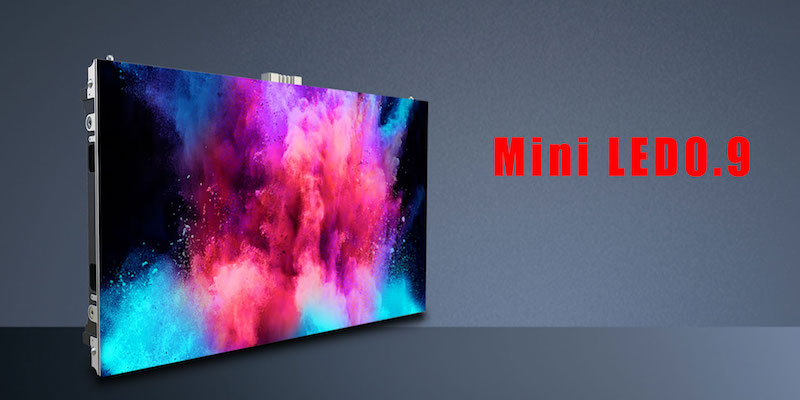
Point A. Small pixel pitch LED screen market capacity continues to expand
The emergence of small pixel pitch technology has promoted the expansion of LED display to indoor ultra HD applications. At present, esdled small pixel pitch LED displays are mainly used in high-end large-scale conferences, international exhibitions, large-scale shopping malls, radio stations, studios, and other indoor venues. With the maturity of small-pitch display technology in recent years, and the rapid development of smart cities and safe city projects, the demand for high-end customized display projects from smart transportation, security monitoring, and military command centers is growing. The high-pitched, high-brightness, seamless splicing and other unique advantages of the small-pitch LED display to bring a broader market space. According to incomplete statistics, the indoor small-pitch market regulation in 2018 is close to 2.1 billion US dollars, with an annual growth rate of 39%, mainly due to the growth of demand in the high-end indoor display market.
For this reason, Eastar has introduced a mini 4-in-1 small pixel pitch VE LED display to meet the growing needs of customers. Easy-to-reach small-pitch VE LED display features high-brightness and low-gray, dual-power backup, wireless Connected, using exclusive HCC technology, and won the German Red Dot Industrial Design Award, a number of well-known TV stations including Hong Kong TVB adopted Eastar's small pixel pitch display system. In the future, small-pitch LED displays will continue to shift to greater density, towards smarter and more standardized, and Eastar will follow the pace of industry development to further expand the small pixel pitch LED display market.
The development of emerging technologies such as AI, VR, and face recognition is becoming more mature, and the small pixel pitch LED display market will be further opened, and the application field will be further subdivided. To this end, Eastar's R&D team adheres to customer satisfaction as the first standard and strives to develop a Mini 0.9 LED display. It has an ultra-narrow pitch of 0.9mm and supports 4K ultra-high definition display. It is very suitable for indoor use. HD display scenes. Nowadays, China's new retail development is very fast. Small pixel pitch LED display can realize the development of smart retail through the combination of overlay interaction, big data cloud operation, and VR technology, creating better visual, shopping experience and retail storefront for customers. The opportunity to upgrade, at the same time, the combination of the two also created a larger incremental market for small pixel pitch LED displays.
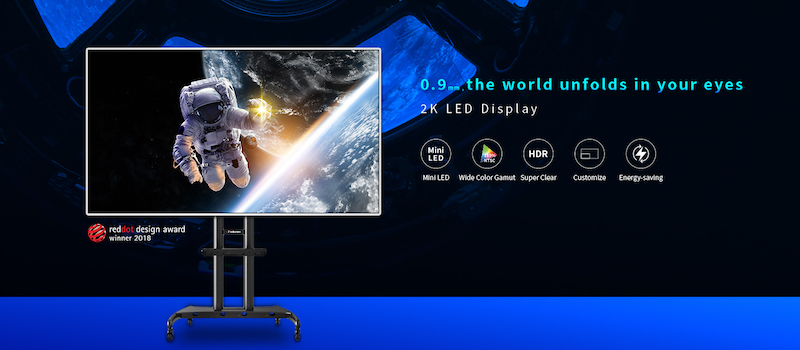
In addition, with the decline in the research and development cost of small pixel pitch LEDs, its application fields have further expanded, and it is no longer limited to indoor applications and has begun to expand into outdoor fields such as media advertising and landscape lighting. For example, in urban squares, large commercial centers, landmark buildings, railway stations, airports, sports and cultural venues, etc., you can see small outdoor spaces, combined with naked-eye 3D, smart touch, Internet + and other technologies, outdoor Small pixel pitch LED displays will open up a larger application market.
Point B. Technological Innovation Brings Application Innovation, Mini/Micro LED is Ready to Go
In 2018, the packaging technologies such as Mini LED and Micro LED have made substantial progress. The small pixel pitch density, cost performance and stability of small-pitch LED display screens have made a qualitative leap, attracting many LED display companies.
At present, the distance between most small-pitch products is between P1.2-P2.5 and has entered the stage of homogenization competition. In order to open the gap with competitors, some enterprises with research and development strength have begun to “0.9. With the development of “0.9 pitch” direction, domestic high-end LED display manufacturer Shenzhen Eastar Electronics Co., Ltd. has developed Mini 0.9 small pixel pitch display to improve the competitiveness of enterprises and better service to customers.
The COB (chip on board) technology was developed for ultra-small pixel pitches below P1.0. Mini LEDs and even Micro LEDs have taken another innovative direction. SMD and COB are both single-lamp beads on the patch, and Mini/Micro LEDs are oriented in the package. For example, the currently commonly used "four-in-one" Mini LED packs four sets of RGB crystal particles in a single bead and then use a patch process to make the display.
This innovative idea brings obvious advantages, showing that the basic unit is more compact, reaching the level of crystal particles, without the need for traditional packaging operations at the crystal grain level, which reduces the process difficult to some extent, but the process is difficult. Solving takes time. The development of the Mini/Micro LED can expand the application range of small pixel pitch LEDs, ranging from VR glasses and smart watches to TV screens and giant screen theaters. The industry is generally optimistic about the future development of Mini/Micro LEDs. Today, Taiwanese panel makers have begun to work in the field of Mini LEDs, and backlight applications are about to land; in addition, Samsung, Sony, and other "non-traditional" small pixel pitch LED screen manufacturers have introduced Micro LED prototypes to seize the first-mover advantage.
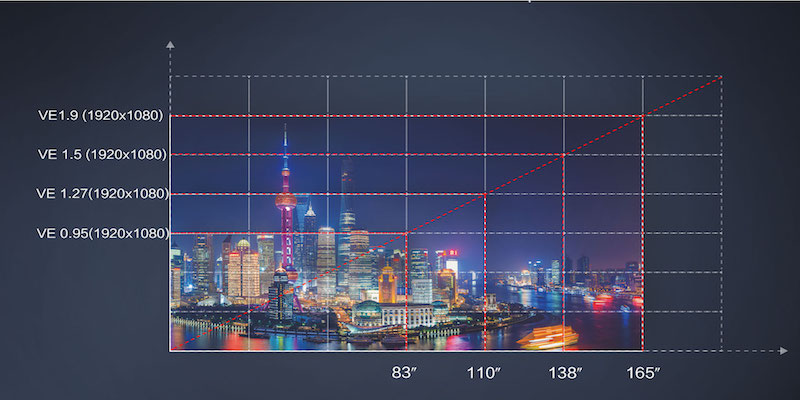
Point C. The Market Structure is Changing. Enterprises at Home and Abroad Competition is Heating Up.
In 2017, Chinese manufacturers occupied the top six in the revenue ranking of small pixel pitch LED displays. The market share of the top eight manufacturers in the world was 72%, and the industry concentration was high, showing a high-concentration and oligopolistic market in China. With the maturity and application of Mini/Micro LED technology in the past two years, the market pattern of small pixel pitch LED display has begun to change. In the field of ultra-small pitch (≤P1.0) display, in addition to China's domestic leading companies have launched related products. International manufacturers such as Samsung and Sony have also begun to deploy in the ultra-small pixel pitch market, and have developed new products in advance through strong capital and years of precipitation technology to seize market voice.
Under the enthusiasm of leading enterprises at home and abroad to rush to small-spacing emerging markets, most small and medium-sized enterprises in China are in a wait-and-see state for new technologies, and they dare not act rashly. On the one hand, in order to lay out the hot and small gap market, whether it is equipment introduction or product development, these small and medium-sized enterprises have invested huge sums of money, they do not have a strong financial background to support the research and development of new technologies. On the other hand, from the current Mini/Micro LED products on the market, it is still only the initial test stage, and there are problems such as high cost and not suitable for long-term viewing. Whether it can be favored by the market is still unknown, small and medium-sized small spacing Enterprises do not dare to take this risk, and they cannot afford the consequences of failure.
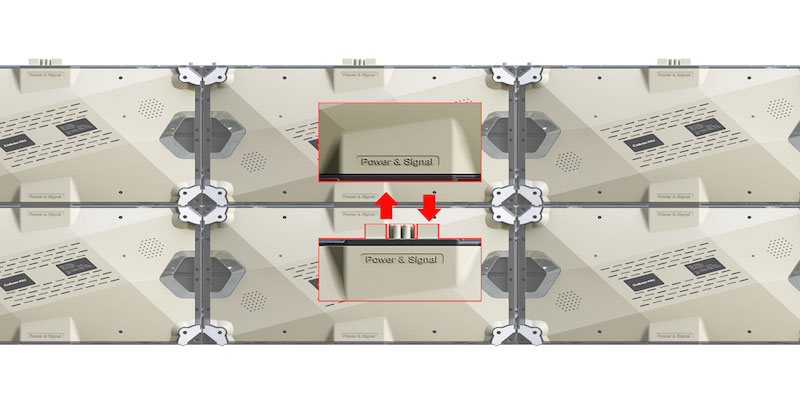
It is true that the starting point of new technologies and new products is driven by the leading enterprises in the industry. Under the joint efforts of domestic and foreign companies, we are fortunate to see that the problems of Mini/Micro LED technology have been overcome. It is estimated that in 2019, Mini LED will reach a market scale of US$1.6-1.8 billion. The market size of Micro LED is expected to reach 100 million yuan. By 2025, the size of Micro LED market will reach 4.9 billion yuan, accounting for half of the small-pitch industry.
In summary, the small-pitch LED display market will become a must for all LED screen manufacturers. Enterprises must keep up with technology trends and trends, and adopt appropriate strategies to meet the changes brought about by new technologies based on their own market positioning and goals. And the challenge to seek more room for development. Showing the beauty of the world is the mission of Eastar. With the small pixel pitch display of VE Mini 4-in-1 HCC technology, in the future, Eastar has the confidence to have a place in the small pixel pitch LED display market.